By Kim Erle and Louis Caiola
Wood. It's Everywhere. Wood pilings. Wood framing. Wood sub flooring. Wood sheathing. Wood flooring. Wood cabinetry. Wood paneling. Wood doors. Wood shingles. Wood roof. Wood decking.
Deforestation has been found to be responsible for 20-25% of global warming
According to the World Preservation Foundation, “deforestation has been found to be responsible for 20-25% of global warming, due to the massive release of CO2 that had been captured and stored in the trees. To get a picture of just how much CO2 is being released, deforestation releases as much CO2 into the atmosphere in one day as would 8 million people flying from London to New York.”
With so much wood integrated into the Sunset Green Home project, we've given a great deal of thought to where our wood components come from and what we can do to minimize our impact on the environment.
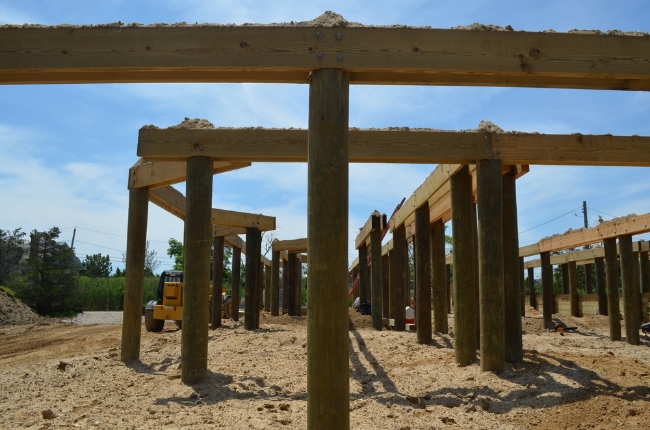
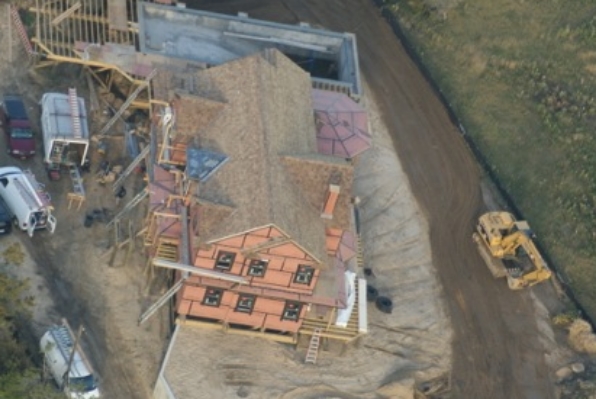
Here are some of our strategies:
- The LEED for Homes program prohibits the use of tropical hardwoods that do not carry Forest Stewardship Council (FSC) certification. There's a reason many people choose tropical hardwood for exterior decking. These woods are not only beautiful, but they hold up well over time. However, according to a report by the Union of Concerned Scientists, "15 percent of annual anthropogenic (human-caused) carbon emissions come from tropical deforestation." FSC certified wood products come from well-managed forests whose owners go through rigorous certification and continuous oversight to ensure minimal environmental impact. Sunset Green Home selected Walk Green Products' FSC-certified cumaru, which was provided by Sterritt Lumber, a 2014 recipient of the FSC Leadership Award.
- Nantucket Beadboard medium density fiberboard (MDF) paneling and Tru-Stile MDF doors will also contribute to the project's LEED credits. MDF contains nearly 100% recycled content. It comprises sawdust wood fibers recaptured from sawmill waste. But not all MDF is sustainable. To manufacture MDF, wood fibers are bound together with binders and resins - and those inputs still typically contain formaldehyde, a known carcinogen. Sunset Green Home's team specified no added urea-formaldehyde MDF for both the doors and the paneling, which makes our MDF products recyclable at the end of their useful lives and - just as importantly - allows them to contribute to a healthy indoor environment.
- The kitchen and other millwork in the home have been constructed from Decospan's Shinnoki and Querkus products. Decospan is dedicated to environmental stewardship and healthy products. Shinnoki veneers are FSC certified, as is the MDF used in the base boards. The adhesives and finishes contain zero VOCs and are manufactured without added urea-formaldehyde.
- Sunset Green Home's ZIP System sheathing and AdvanTech sub-flooring qualify for LEED credits in the program's Materials & Resources credit category because the wood used in both systems was grown, extracted and processed within 500 miles of the project. The same goes for the pilings that support the house. By using regionally grown and processed wood products, we are reducing the environmental impact from transportation.
- The country grade wide plank white oak floor is gorgeous and sustainable. Woodwrights Wide Plank Flooring is a local company whose mill is only 15 minutes from Sunset Green Home. The floors were milled and finished locally, which minimized the cost and impact from transportation.
- We chose Certi-Label taper sawn western red cedar roof shingles supplied by Anbrook Industries and Certi-Label side wall shingles supplied by Liberty Cedar. The Cedar Shake & Shingle Bureau's Certi-Label program ensures that the shingles meet third party quality and sustainability standards. Sunset Green Home's use of thicker taper sawn shingles, while slightly more expensive than more commonly used Perfection shingles, means that our roof will last longer. And a longer life means less waste over time. We met with Brooke Meeker, Anbrook's CEO to discuss her company's products. Watch our video interview of Brook to learn why sustainable forestry is so important.
You can probably tell that we undertook a tremendous amount of research to get Sunset Green Home's wood products sourcing right. It's important to know where your wood products come from. The next time you're in the market for building materials, furniture or other wood products, take a moment to learn where they come from. You’ll be armed with the information you need to make a sustainable choice!